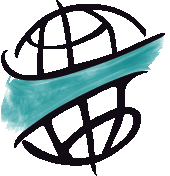 |
Tropentag, September 20 - 22, 2017 in Bonn
"Future Agriculture: Social-ecological transitions and bio-cultural shifts"
|
An Optimised Solar Camel Milk Powder Processing Plant for Rural Arid and Semi-arid Regions
Jackline Akinyi Ogolla1, Christian Dede1, Steve Meyers2, Bastian Schmitt2, Michael Okoth3, Oliver Hensel1, Barbara Sturm4,1
1University of Kassel, Agricultural and Biosystems Engineering, Germany
2University of Kassel, Department of Solar and Systems Engineering, Germany
3University of Nairobi, Food Science, Nutrition and Technology, Kenya
4Newcastle University, School of Agric., Food and Rural Developm., United Kingdom
Abstract
Kenya's camel milk industry contributes significantly to the economic and nutritional safety of the population located in the arid and semi-arid areas (ASALs). Due to the inadequacy of preservation technologies, the production and consumption of milk are limited to this group. Processing the milk into powder is one approach for the extension of shelf life. This process is very energy intensive. The exemption from Value Added Tax on solar products by the Kenyan government coupled with high solar irradiation in the region provides an alternative energy source. This study, evaluated the feasibility and design of an energy efficient and solar assisted milk processing plant for decrease of post-harvest losses, greenhouses gas emission reduction and efficient energy utilisation.
The reference values used in the computation of the energy consumption of the milk powder and butter were based on prior fieldwork. Initially, the process was characterised and optimised, the energy targets redefined the energy targets and multiple solar integration points were analysed. The analytical tools included: mass & energy balance; Pinch analysis, simulation of solar thermal and analysis of the economic feasibility.
The analysis showed that a significant amount of cream is produced during milk powder processing line, and to limit its wastage, the excess cream is channelled for butter processing. In optimising the process, a resequence design was the most economical, having the energy requirement for the processes decreases by approximately 46.1 %. This required an increased investment cost for heat exchanger integration. Moreover, the amount of water used decreased by approximately 50 % per litre of processed milk. For processes below 90°C that utilises hot water, which is approximately 85.5% of the total energy demand, could best be met with evacuated tube collectors. For chilling, cooling and mechanical processes solar photovoltaics was utilised. For the highest energy demanding process, spray drying, the air was first preheated by exhaust air from the process, then preheated to 90 °C by solar thermal and finally indirectly heated by a fuel oil boiler.
In conclusion, an optimised hybrid system of fuel oil and solar energy is proposed for the ASAL milk powder processing plant.
Keywords: ASALs, butter, camel milk powder processing plant, process optimisation, solar thermal energy
Contact Address: Jackline Akinyi Ogolla, University of Kassel, Agricultural and Biosystems Engineering, Nordbahnhof Str.1a, 37213 Witzenhausen, Germany, e-mail: ogollajackline rocketmail.com
|