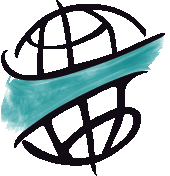 |
Tropentag, September 20 - 22, 2017 in Bonn
"Future Agriculture: Social-ecological transitions and bio-cultural shifts"
|
Pineapple Processing in Central Uganda
Emmanuel Wokulira Miyingo1,2, Oliver Hensel2, Barbara Sturm3
1Makerere University, Dept. of Electrical and Computer Engineering, Uganda
2University of Kassel, Agricultural and Biosystems Engineering, Germany
3Newcastle University, School of Agric., Food and Rural Developm., United Kingdom
Abstract
Pineapples, like many fruits, are highly perishable and require either immediate consumption or processing and/or refrigeration for later consumption. The perishability of fruits leads to high post-harvest losses (over 50% in Uganda). To improve pineapple shelf life and quality, four major processes are being employed in Uganda: processing into juice, wine, local drink (munaanansi), and dry products. Our research assesses each of the processes to determine current practices in relation to energy and water utilisation, and fruit wastages. The objective is to better understand the present state so to guide resource optimisation, efficiency, and sustainability. Here we present results from studies on drying and munaanansi production in central Uganda for data collected (Nov 2016 - March 2017) within three districts (Kampala, Wakiso, and Kayunga). One drying company/cooperative was selected from each district. Modern hybrid dryers are employed by companies selected in Kampala and Wakiso while the Kayunga Cooperative owns ordinary solar thermal dryers. The Kasangati, Wakiso Company runs dryers on solar, mains, biomass, diesel, and petrol, while the Kawempe, Kampala Company runs on mains and biomass. The average inlet and exit temperature for one drying unit in Kasangati is 69.50°C and 47.11°C respectively, while the inlet and exit for one drying unit in Kawempe is 118.26°C and 59.20°C respectively. Relatedly; the average inlet and exit temperature for dryers owned by Kangulumira Cooperative is 44.20°C and 45.50°C respectively. On average; Kasangati Company requires 10.89 kWh electrical energy and 2.48 kg of biomass to produce 1 kg of dry pineapples, while the Kawempe Company requires 3.07 kWh electrical energy and 3.48 kg of biomass to produce 1 kg of dry pineapples. Munaanansi production is generally individual/family business; so six individual/family munaanansi producers were selected from Kampala where the drink is most popular. Firewood and charcoal are the main fuels while pineapples/pineapple peels are main raw materials. On average; 0.20 kg of pineapples/peels, 0.21 kg of biomass, and 1.04 L of water produce 1 L of munaanansi, yielding 0.15 kg of waste. Great potential for the optimisation of energy, water, and pineapples exists in these processes.
Keywords: Biomass, dryers, munaanansi, optimisation, perishable, solar
Contact Address: Emmanuel Wokulira Miyingo, Makerere University, Dept. of Electrical and Computer Engineering, Makerere, Uganda, e-mail: miyingo yahoo.com
|